Keeping your mud and fracturing pumps in top condition is crucial for ensuring optimal performance and maximizing the efficiency of your operations. Regular maintenance and proactive care can extend the lifespan of your equipment, reduce downtime, and improve overall productivity.
One of the key aspects of maintaining your mud and fracturing pumps is to closely monitor their performance and address any issues promptly. This includes regularly checking for signs of wear and tear, such as leaks, vibrations, or unusual noises, and addressing them before they escalate into more serious problems.
Proper lubrication is also essential for the smooth and efficient operation of your pumps. Ensure that you are using the recommended lubricants and that they are applied at the recommended intervals. Neglecting this can lead to increased wear and tear, reduced efficiency, and even premature failure of critical components.
Additionally, it’s important to keep your pumps clean and free of debris. Regularly cleaning the suction and discharge valves, as well as the impellers and other moving parts, can help maintain optimal performance and extend the lifespan of your equipment.
By following these best practices and prioritizing the maintenance of your mud and fracturing pumps, you can ensure that your operations run smoothly and efficiently, maximizing your productivity and profitability.
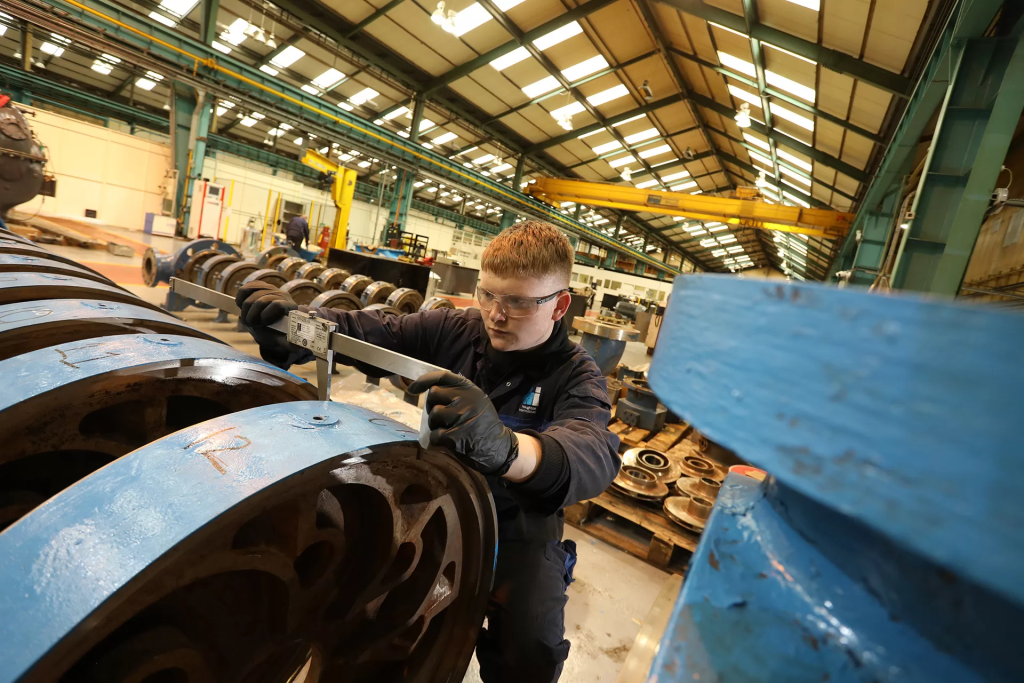
1. Conduct Regular Inspections
Perform daily visual checks for signs of wear and tear, potential leaks, and any loose connections that may develop over time. It is essential to focus on key areas of the equipment, including the fluid end, valves, and gaskets, as these components are critical to ensuring optimal performance and preventing any operational issues. Regular inspections will help identify any problems early, allowing for timely maintenance and repairs, thereby extending the lifespan of the machinery.
2. Monitor Fluid Levels
Hydraulic oil and lubrication levels should be kept within the manufacturer’s recommendations to prevent overheating and premature wear.
3. Replace Wear Parts Proactively
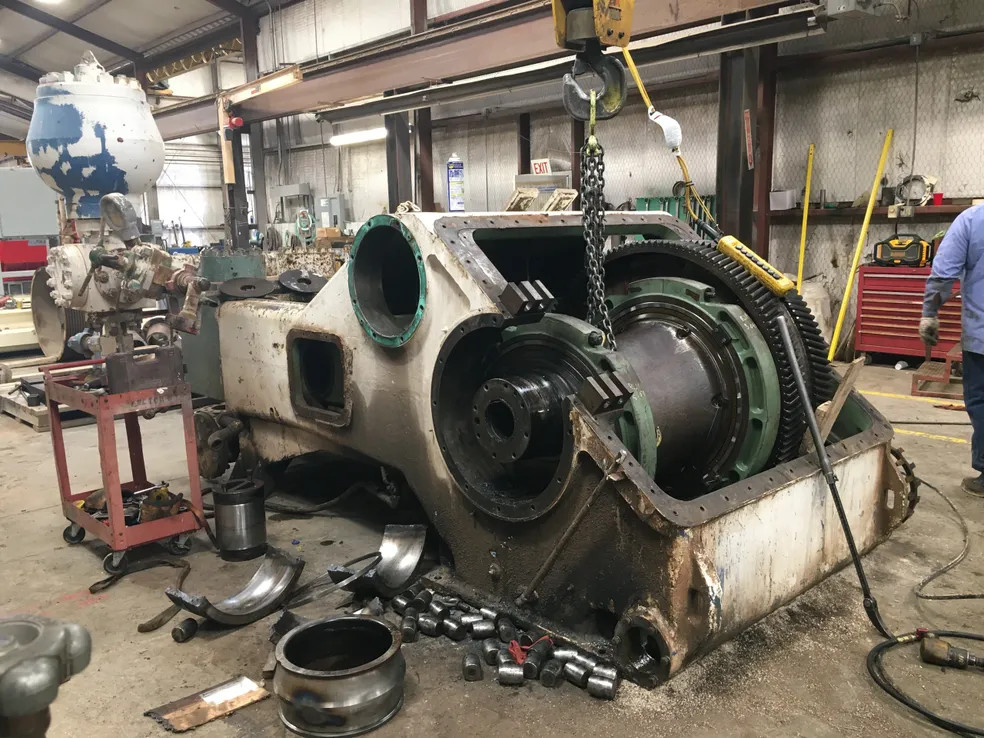
Components such as plungers, seals, and valves are consistently subjected to significant levels of stress during their operational lifetime. To prevent unexpected and potentially costly failures, it is crucial to replace these components based on the number of usage hours they have accumulated. Regular monitoring and timely replacement can greatly enhance the efficiency and longevity of your equipment, ensuring it operates smoothly without the risk of sudden breakdowns.
4. Check for Proper Alignment
Misalignment between the pump, motor, and drivetrain can lead to vibrations, inefficiencies, and long-term damage.
5. Flush the System After Use
Pumping abrasive or chemically reactive fluids can leave residue that degrades equipment. Flushing with clean water or appropriate cleaning agents extends the pump’s life.
6. Maintain a Spare Parts Inventory
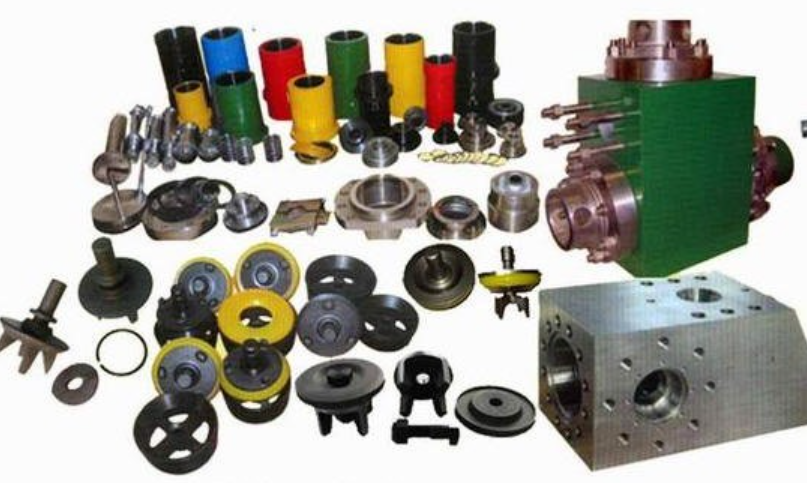
Having essential spare parts readily available, such as packing kits and valve assemblies, is crucial for minimizing downtime during repairs and maintenance work. By ensuring that you have these important components on hand, you can swiftly address any issues that arise, thereby enhancing operational efficiency and reducing the overall impact on your workflow.
7. Train Your Team
Operators should understand pump operation, maintenance schedules, and troubleshooting to address minor issues before they escalate.
8. Invest in Predictive Maintenance Tools
Use IoT-enabled sensors or vibration analysis to detect early signs of pump degradation and plan timely interventions.
Proper pump maintenance doesn’t just enhance efficiency but also extends the equipment’s lifespan, reducing operational costs and ensuring reliability in the field. For expert advice or to explore high-performance mud and fracturing pumps, contact us today!